Application Examples
Cutting Tools
In the field of cutting tools, PVD coating improves the service life and machining efficiency of tools.
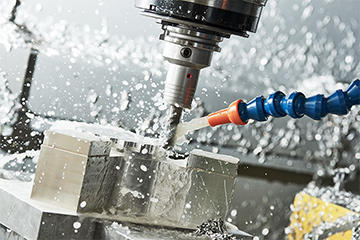
Improving the service life of tools
Cutting high-hardness metal used in automobiles, aircraft, and bridges (such as titanium alloy and Inconel) requires high-speed, high-temperature machining, which can quickly damage tools. PVD coating is used to maintain tool
performance even in these severe environments. In addition, PVD coating is also effective when machining metal material that is softer than titanium alloy and Inconel.
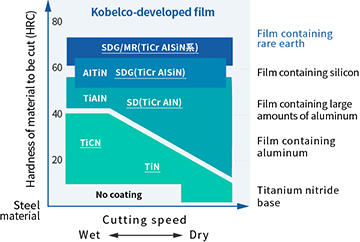
Improving machining efficiency
PVD coating can be used to improve the wear and heat resistance of tools for faster cutting, thereby reducing the machining time. In addition, PVD coating can help solve issues such as adhesion of cuttings that occurs when machining aluminum and other soft materials. This enables continuous machining, and an increase in machining efficiency and a reduction in maintenance costs can be expected.
Kobelco has abundant knowledge and a track record of solutions for surface treatment of cutting tools, and we can provide the optimal film according to your tool type and machining conditions.
Main Applications
Drills
Cutting Alloys
In recent years, there has been an increasing shift from high-speed steel drills to carbide drills due to lower tool machining costs. However, while carbide drills are high speed, highly accurate and offer improved finish roughness, they are prone to chipping and defects.
Kobelco has solved this with a multilayer film (VS/MR film). By controlling the defect resistance of carbide drills, which is their disadvantage, both machining efficiency and durability can be improved.
* Depending on machining conditions, film other than VS/MR film may be more effective.
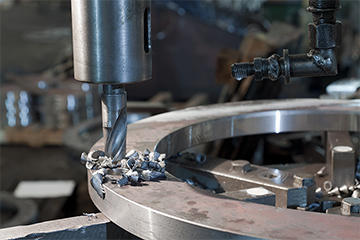
Data on Carbide Drill Machining
Tool: ø6 carbide drill (with oil hole)
Material to be cut: Alloy steel (SCM440)
Cutting speed: 75 m/min, Feed rate: 0.18 mm/rev
Machining depth: 29 mm, Coolant: Wet
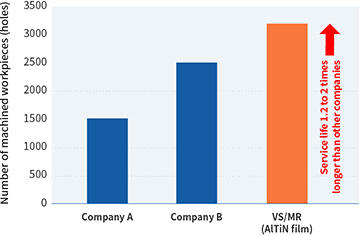
Kobelco Technology
Optimizing the aluminum titanium nitride film can improve adhesion and defect resistance, greatly improving the cutting efficiency.
Recommended Film and Equipment
Film
Equipment
Endmills
Cutting Dies
Hardened steel used for dies is extremely hard (HRC55), and the tool for machining needs to have a hardness more than three times that. Also, because dry cutting is performed without using oil, the temperature of the tool can increase to high levels, creating a harsh cutting environment.
Kobelco developed its own film (SDG/MR film) that solves these issues at a high level. Adding multiple elements improves the oxidation and wear resistance and enables operations that are three or more times faster (max. rotation speed of 600 m/min) than general-purpose coating film (titanium aluminum nitride film).
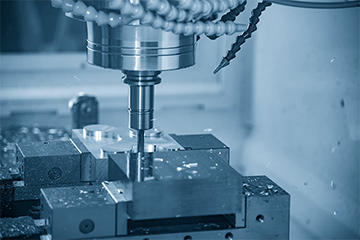
Data on Ultra-high Speed Milling of Hardened Steel
Tool: ø10 carbide ball endmill
Material to be cut: Die steel (HRC55)
Cutting speed: 300 to 600 m/min, Feed rate: 0.06 mm/blade
Shaft cutout: 5 mm, Diameter cutout: 0.6 mm, Coolant: Dry
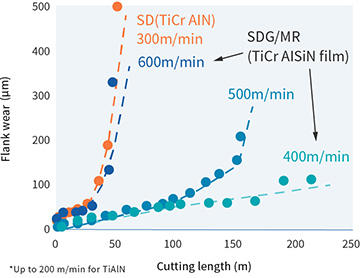
Kobelco Technology
Elements are added to improve resistance to oxidation and wear. This enables a processing speed at least three times faster than general-purpose coating film.
Cutting Aluminum Alloys
Recently, automobile parts using aluminum have increased due to lighter weight automobiles. Alongside this, the need for cutting aluminum alloys is also increasing. However, when a cutting tool featuring a coating film with high friction coefficient is used to cut aluminum alloy—a soft material—the tool may adhere to the material being cut.
To solve this problem, Kobelco developed a carbon evaporation source for ta-C coating that can achieve high hardness at the same time. Film formation using ion plating has a high adhesion and excellent performance when cutting aluminum.
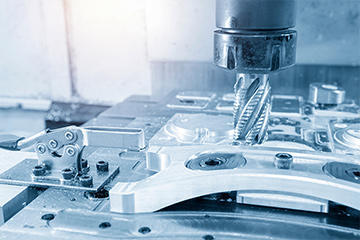
Data on Aluminum Alloy Machining Using ta-C
Tool: ø10 carbide endmill
Material to be cut: Aluminum alloy (A7075)
Cutting speed: 377 m/min, Feed rate: 0.11 mm/blade
Shaft cutout: 5 mm, Diameter cutout: 0.5 mm, Cutting length: 5 m
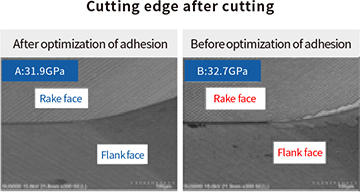
Kobelco Technology
Optimizing the deposition conditions can improve adhesion. By controlling the peeling of the film, tool replacement and other losses can be reduced.
Recommended Film and Equipment
Film
Equipment
Inserts
Cutting Inconel
In the aircraft and thermal power generation fields, there are increasing cases where alloys with high heat resistance are used in gas turbines to improve fuel efficiency. There is also a growing number of cases where metal material with extremely high hardness such as Inconel is used, and the required standard for tools is also increasing.
To meet these needs, Kobelco developed SDG/MR film to achieve high hardness and oxidation resistance. This is used in surface treatment of carbide inserts.
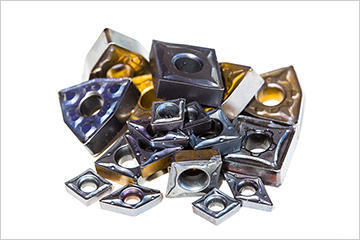
Data on Carbide Insert Machining
Tool: Carbide insert
Material to be cut: Inconel
Cutting speed: 40 m/min, Feed rate: 0.125 mm/rev
Machining depth: 0.25 mm, Coolant: Wet
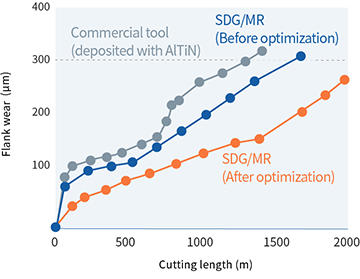
Kobelco Technology
Optimizing SDG/MR film can improve adhesion and wear resistance. There is less wear than general aluminum titanium nitride film, and peeling of film at the start of cutting can be controlled.
Cutting Chromium Molybdenum Steel
Tools for machining high-hardness materials of HRC60 or higher require an extremely hard coating film. While diamond-like carbon (DLC) coated tools and diamond tools are effective in that they have a high hardness, the carbon, which is the main component, has a higher reactivity to iron, so they are not suitable for machining iron materials. Meanwhile, CBN sintered tools use a material that has both high hardness and low reactivity to iron, but as the temperature increases during cutting, the base material oxidizes, shortening the service life of the tools.
To solve these issues, Kobelco developed SDG/MR film, a coating film that is carbon free and is strong against oxidation. This is also used in cutting tools for cutting chromium molybdenum steel, Inconel, and other materials that are difficult to cut.
Data on Carbide Insert Machining
Tool: CBN insert
Material to be cut: Chromium molybdenum steel (HRC60)
Feed rate: 0.12 mm/rev, Machining depth: 0.1 mm
Cutting length: 2 km, Coolant: Wet
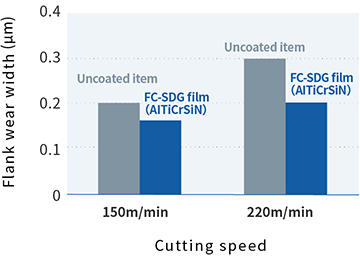
Recommended Film and Equipment
Film
Equipment
Hobs
Cutting Alloy Steel (SCM)
A high-speed steel (HSS) hob is a tool used to make gears used at manufacturing sites for automobile parts. When performing high-speed cutting with this HSS hob, the temperature of the blade edge increases, and depending on the situation, a tempering process may be required.
To reduce this process loss, Kobelco developed NS/R film, a film with a low thermal conductivity. This film significantly controls the temperature rise of the substrate compared to general-purpose aluminum chromium nitride film, and a proprietary preprocessing is performed, thereby achieving high adhesion to the substrate.
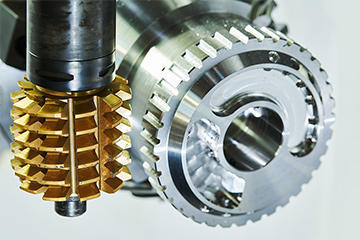
Data on Hob Cutter Machining
Tool: HSS hob cutter
Material to be cut: Alloy steel (SCM)
Cutting speed: 75 m/min, Feed rate: 1.5 mm/rev
Coolant: Wet
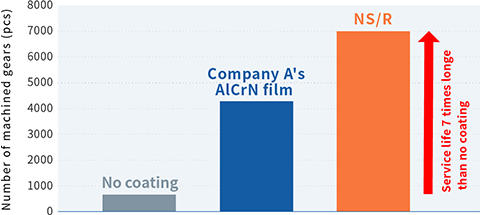
Kobelco Technology
Optimal elements are added to improve resistance to oxidation, wear, and defects. By controlling the deterioration of tool performance, the number of machined workpieces has been significantly improved.
Recommended Film and Equipment
Film
Equipment
Taps
A tap is a tool used to cut female threads and requires high precision.
Kobelco's Super Cathode is an evaporation source with excellent smoothness, and by coating the surface of the tap with this evaporation source, cutting can be performed with greater precision and efficiency than methods using a hollow cathode.
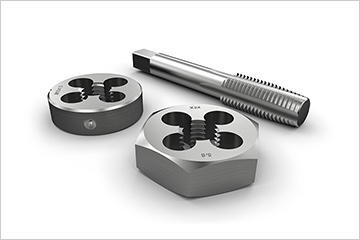
Data on Tap Machining
Tool: HSS tap (M8)
Material to be cut: SUS316L
Cutting speed: 16 m/min
Coolant: Wet
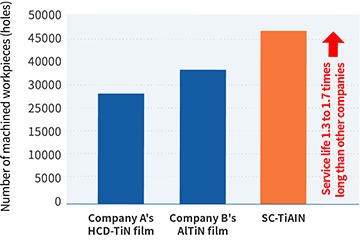
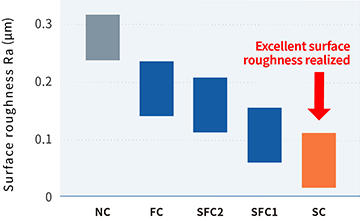