Film Properties
NS/R (Titanium Chromium Aluminum Nitride Multilayer)
NS/R film is formed from two layers with different functions to achieve high toughness, adhesion, high hardness, and oxidation resistance.
Film construction
Topcoat: Film with high hardness and excellent oxidation resistance
Middle layer: Film with high toughness and adhesion
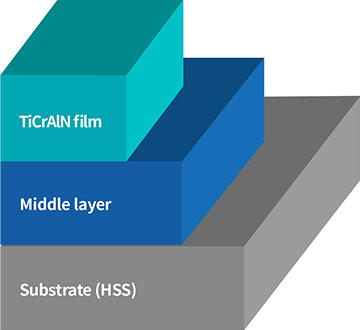
Recommended Applications
• Hobs
• Turning inserts
• Milling inserts
Application Examples
HSS Hob
The hob, a cutting tool for manufacturing gears, and other HSS tools experience high temperatures due to friction during dry cutting, and excessive temperature rises can cause deterioration of blade edge performance. To solve this issue, Kobelco developed a new film (NS/R film) with four functions: controlling thermal conductivity, improving oxidation resistance, enhancing adhesion by special pretreatment, and reducing film stress. Cutting using a hob reduces process loss and improves productivity.
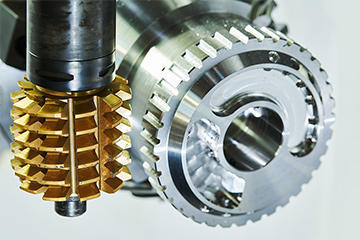
Controlling Thermal Conductivity
NS/R film has a thermal conductivity of 1 W/mK or lower. This makes it possible to more effectively control temperature rise of the substrate (HSS) than with a surface treatment using a general-purpose film such as TiAlN film.* TiAlN film has a thermal conductivity of 6 W/mK.
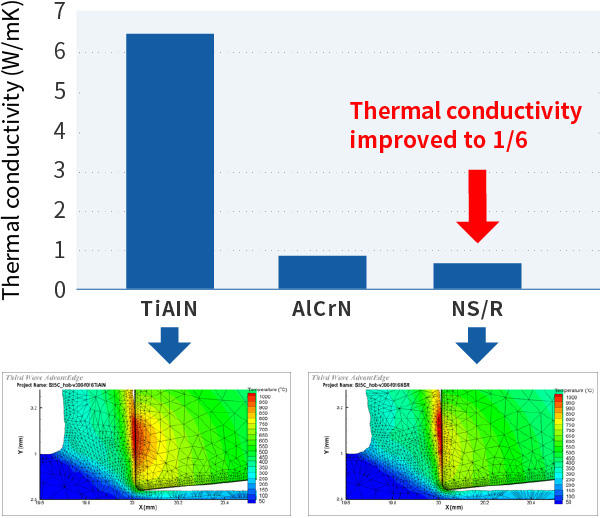
Improving Resistance to Oxidation
In oxidation weight tests, NS/R film was stable at or below a temperature of 1200°C, and it showed a high resistance to oxidation.* TiAlN film and AlCrN film become unstable when the temperature exceeds 800°C.
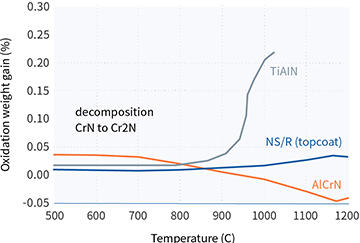
Using Special Pretreatment to Improve Adhesion
A mixture of water and abrasive (slurry) is sprayed with compressed air onto the surface of the substrate. This blasting prior to deposition improves adhesion of the film.
Using SFC Evaporation Source to Reduce Film Stress
Compared to the FC or SC evaporation sources, the SFC evaporation source can reduce film stress. Selecting the appropriate film and combining this with the SFC evaporation source improve the service life of the coating.
Cutting Test Result
Using the SFC evaporation source to reduce film stress and providing special pretreatment improve both adhesion and service life.
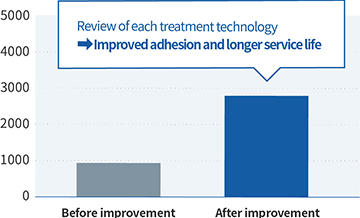
Cutting Test Result
TiAlN film reaches the end of its service life (200 μm) at a cutting distance of 10 m. In contrast to this, NS/R film has wear of 100 μm or less even at a cutting distance of 40 m. A significant increase in service life was confirmed.
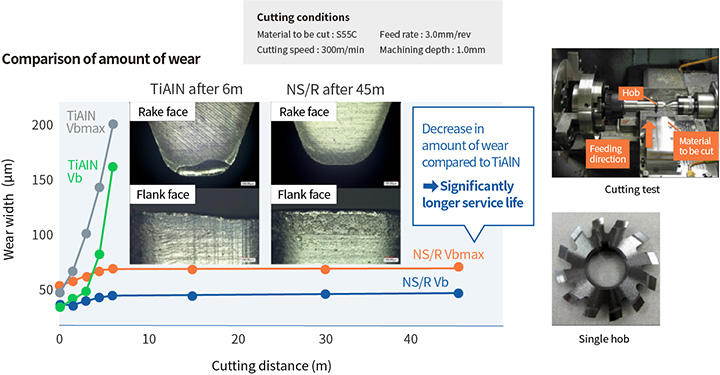