Overview of Equipment
UBMS® Series
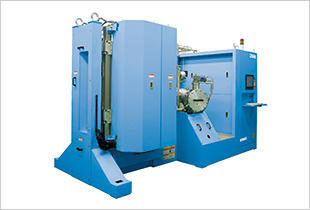
The Unbalanced Magnetron Sputtering System (UBMS®) Series is mainly used by customers in various industries
including parts, tools, dies, and molds as diamond-like carbon (DLC) film coating system.
The properties of DLC film can easily change depending on the deposition method and processing temperature, but
we have solved this problem using our many years of experience and knowledge. We can also provide solutions for
adhesion of DLC film, which has long been an issue.
Equipment Features
The UBMS® Series is sputtering equipment equipped with an evaporation source developed in-house by Kobelco. The magnetic field configuration is optimized to strengthen plasma at deposition and improve the ion assist effect, which is effective for film quality control. As a result, film with good surface roughness can be achieved.
Details of evaporation sourcesIt is possible to form a film to improve adhesion by sputtering, and processing can also be performed using the PE-CVD method for deposition of DLC.
* PE-CVD method: Coating technology that uses gas as the deposition material. Methane and acetylene are mainly used for deposition of DLC film. The PE-CVD method enables deposition five or more times faster than the UBMS® method, thereby improving productivity, which is a problem of the UBMS® method, while maintaining the sliding properties.
Specifications can be customized to meet international safety standards. We can also tailor the specifications to meet your needs for safety standards developed in-house.
Basic Equipment Specifications
![]() |
![]() |
![]() |
![]() |
---|---|---|---|
Minimum space for installation | 4 m × 3.5 m | 5 m × 6 m | 6 m × 7 m |
Effective coating area | ø200 mm × H 120 mm |
ø450 mm × H 400 mm |
ø700 mm × H 800 mm |
Number of evaporation sources | 2 surfaces | 4 surfaces | 7 surfaces |
Substrate table | ø90 × 3 axes, Rotation/revolution | ø130 × 6 axes, Rotation/revolution | ø130 × 12 axes, Rotation/revolution |
Max loading weight of substrates | Max. 20 kg | Max. 180 kg | Max. 360 kg |
Typical application | R&D | Medium-scale production Automobile parts mass production |
Large-scale production Automobile parts mass production |