Film Properties
SDG/MR (Titanium Chromium Aluminum Nitride Multilayer)
SDG/MR film is a film with a titanium aluminum nitride (TiAlN) base and multiple added elements.
In addition to being wear resistant and having excellent resistance to heat and corrosion, and unlike TiAlN film which oxidizes at 800°C, SDG/MR film does not oxidize until 1200°C.
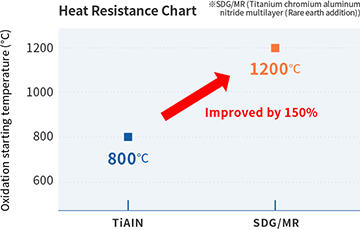
Recommended Applications
・Carbide drills
・Carbide endmills
・Turning inserts
・Milling inserts
・CBN inserts
Application Examples
Cutting Tools for Aircraft Parts
In the aircraft part industry, titanium and Inconel are increasingly used to meet demand for lighter weight fuselages to improve fuel efficiency. However, because these materials are hard and have poor thermal conductivity and high tensile strength, the temperature during cutting tends to rise as does the cutting resistance, making the materials extremely difficult to cut.
Kobelco SDG/MR film features high hardness and excellent oxidation resistance to protect the surface of cutting tools used for difficult-to-cut materials, such as titanium and Inconel, and improves the tool service life.
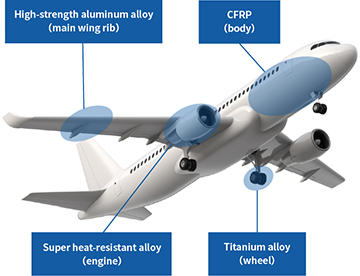
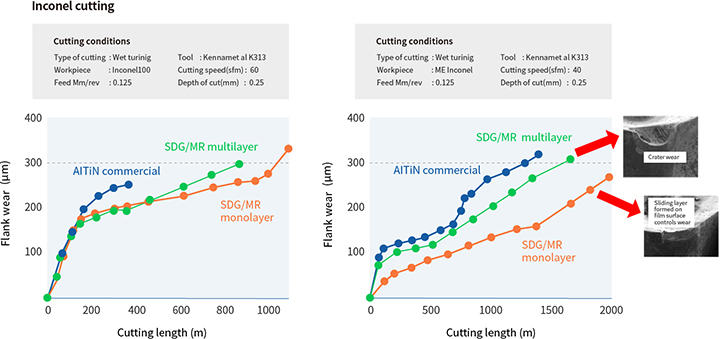
The insert tools were coated and the results of cutting Inconel were compared. When coated with a single layer of titanium aluminum chromium (TiAlCr), crater wear occurred at a cutting distance of 1600 m, but a sliding layer of SDG/MR film controlled wear and provided greater durability.
Cutting Tools for Die Steel
Dies used to machine high-hardness materials such as Inconel also require high hardness, and the tools used to manufacture these dies need an even higher hardness. Kobelco SDG/MR film is used as a surface treatment film for carbide inserts used to machine dies and to improve the service life and reduce maintenance costs of tools.
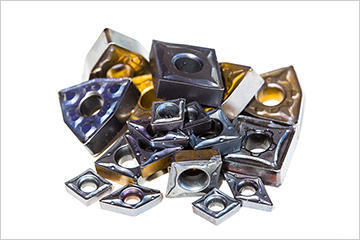
Testing of endmill machining of die steel was performed. When compared to competitors' products, SDG/MR film showed less flank wear.
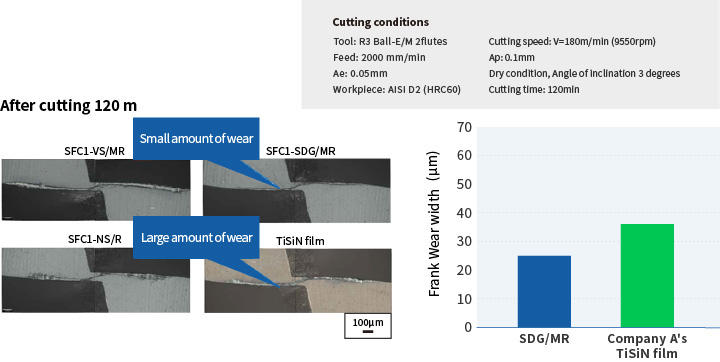
Testing of ultra-high speed milling of hardened steel was performed. TiAlN film reached its limit at 200 m/min, but SDG/MR film was able to perform machining with a rotation speed up to 600 m/min. In addition, at a cutting speed of 400 m/min, wear was controlled to a width of 200 μm or less.
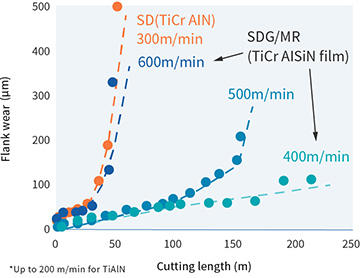