すり減らない。剥がれない。劣化しない。
原子・分子レベルで極限の"強さ"を実現。
「PVD(Physical Vapor Deposition)コーティング」は、原子・分子レベルでの皮膜形成により「高耐久化」、「低摩耗化」、「高寿命化」などを実現する表面処理技術です。
PVDコーティングのプロセス
コーティング対象品(ワーク)の装着
コーティング対象品(ワーク)を、冶具を用いてワークテーブル上に搭載します。
ワーク同士の干渉や処理中の落下がないように注意が必要です。
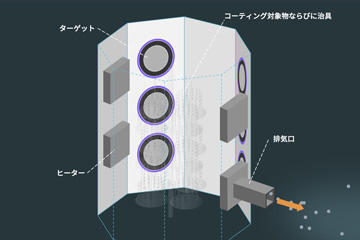
真空処理
処理炉(チャンバー)の中を、コーティングに影響がないレベル(ベース圧)まで真空排気します。炉内に許容量以上の空気が残っていると、次の「ヒーティング」工程でワークの表面に酸化膜が形成され、密着不良の原因になります。
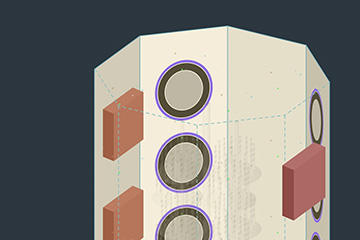
ヒーティング
ワークの表面に付着している不純物(主に水分)を蒸発させます。
ごく微量の水分でも密着不良の原因となるため、炉内の温度を適切に管理・制御し、すべてのワークを十分に加熱します。
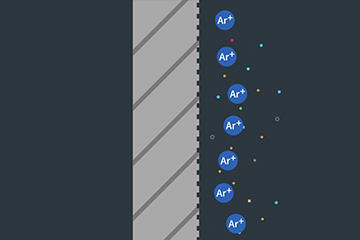
エッチング
ワークの表面にアルゴンイオンを衝突させることで、不純物(主に酸化膜)を除去します。
神戸製鋼所の装置は、強力なArガスプラズマの発生と均一な制御によって、理想的なエッチング効果と優れた皮膜密着性を実現します。
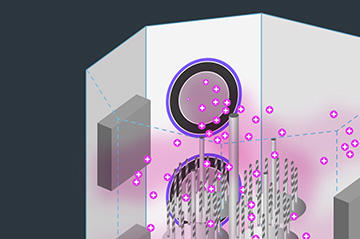
コーティング
コーティング用の金属材料と処理炉(チャンバー)の間でアーク放電をおこなうことで、金属材料が気化してプラズマ状態となり、被膜となる元素がイオン化されます。その後、ワークにマイナスの電圧をかけることで、イオン化した元素がワークに高速で衝突し、皮膜を形成します。
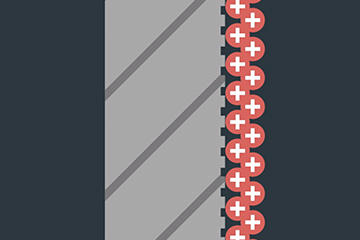
金属材料の種類や処理条件によって、耐摩耗性や耐熱性など、様々な皮膜特性を実現することができます。また、複数の金属材料を用いることで、多元素系の合金膜またはこれらの積層膜の形成も可能。処理炉に注入するガスの種類や量を変えることで、カーボン等のガス元素を加えた成膜も可能です。
冷却・ベント
処理炉内に窒素またはヘリウムを注入し、冷却を促進します。
コーティング対象品(ワーク)の種類によっては変色(テンパーカラーの付着)が発生する可能性があるので、大気を注入するタイミングには注意が必要です。