Film Properties
UB (a-C)
UB film is a diamond-like carbon (DLC) film with ultra high hardness.
DLC film is an amorphous carbon film with diamond-like high hardness and a low coefficient of friction
similar to graphite. It is used in automobile parts under harsh usage conditions.
In addition to the high hardness unique to DLC film, UB film is able to form a smoother film than ta-C film.
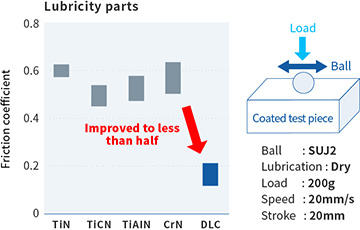
Friction coefficient comparison
Nitride film (CrN, TiAlN, TiCN, TiN): Coefficient of friction 0.4 or higher
DLC film: Coefficient of friction 0.2 or lower
Forming DLC Film
There are three methods of forming DLC film: Unbalanced Magnetron Sputtering (UBMS®), arc ion plating (AIP®), and CVD; UB film is formed using UBMS®.
UBMS®
This method enables the formation of film in the a-C area and gives the film a quality similar to graphite.
By injecting a base gas (hydrocarbon), it is also possible to form a film in a-C:H, which is the area of CVD.
In addition, UBMS® enables the formation of smoother films than AIP® because droplets do not adhere to the substrate
as in AIP®.
CVD
This method enables film formation five or more times faster than AIP® or UBMS®.
Since hydrocarbons such as methane and acetylene are required, hydrogen-free film cannot be formed.
AIP®
This method has a higher ionization rate than UBMS®, thereby enabling the formation of film with diamond-like
hardness.
Since droplets generated from the solid evaporation source adhere to the surface of the substrate, the surface has a
high roughness, and therefore, surface polishing is required after deposition when using it for moving parts. (A
smooth surface can be obtained using UBMS®.)
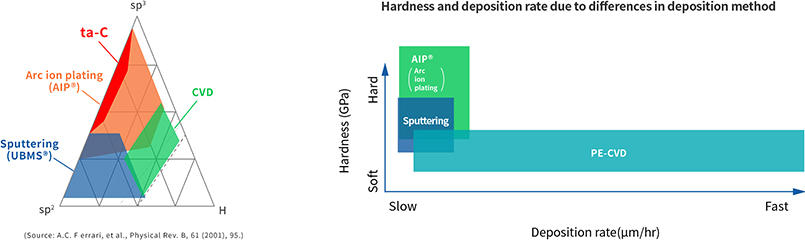
Recommended Applications
• Automobile parts
• Air conditioner compressor parts
• Hydraulic parts
• Machine tool parts, etc.
Application Examples
Automobile Parts
Many automobile and motorcycle parts are used under very rigorous sliding conditions. Among these, engine parts for
race vehicles are made significantly lighter with high output, and extremely high durability is required for sliding
parts.
Diamond-like carbon (DLC) film is indispensable as a solution to create high resistance to seizing and wear even in
high-load conditions from commercial vehicles to race cars.
Patented with DENSO
To provide high adhesion for iron-based substrates, chromium is formed as the ground layer. A WC/WC-C graded layer
is formed on top of this, and it is gradually migrated to a DLC film.
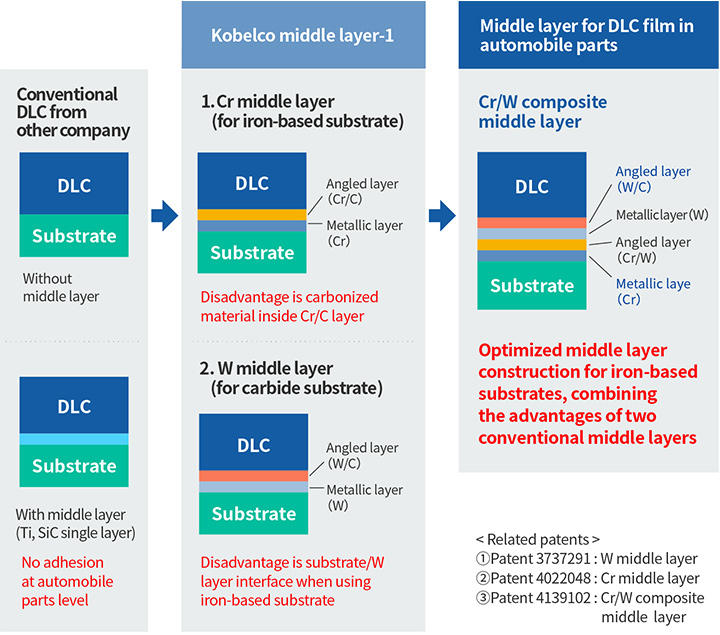
Molds
In the mold field, DLC film with excellent adhesion resistance is used for machining aluminum and copper.
Meanwhile, UBMS®-DLC film is used for perforating punching, which requires impact resistance.
* Compared to an unprocessed punch made of high-speed tool steel (KH material), a punch coated with
nanolayered DLC (BELCOAT® NB) has a service life approximately nine times longer.
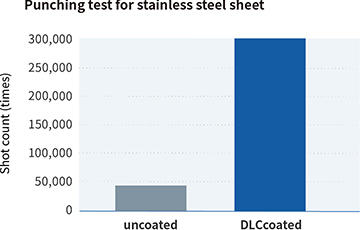
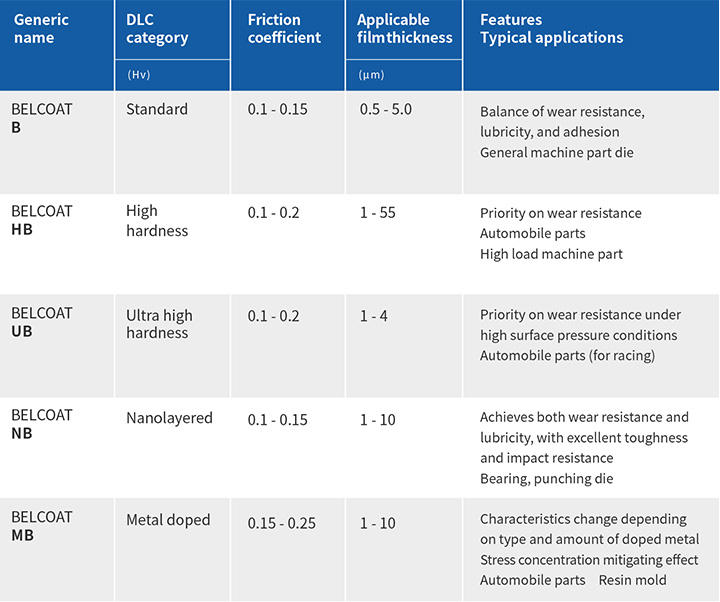